Without doubt, the use of aluminum is increasing within the welding fabrication industry. Manufacturers are often adopting this material, either through innovation, or through pressure applied by their end users. Aluminum's unique characteristics of being light weight, and having excellent corrosion resistance, high strength, high toughness, extreme temperature capability, versatility of extruding, and recycling capabilities make it one of today's favored choices of material for many engineers and designers for a variety of welding fabrication applications. Because of the increased use of aluminum as a manufacturing material, the conversion from steel to aluminum within the welding fabrication industry is becoming increasingly common.
The successful conversion from steel to aluminum welding is largely dependent on the understanding of the fundamental differences between these two materials. I have selected some of the most common problems encountered when moving to aluminum welding such as feedability, porosity, cracking and filler alloy selection.
Crater – A depression in the weld face at the termination of a weld bead. Creep – The slow deformation (for example, elongation) of a metal under prolonged stress. Learn more about Stubby gas lens kits at Scratch Start Tig Tips for getting the most out of your welding practice. One of the best. What you are describing is a weld crater shrinkage cavity, also known as a 'pipe'. Figure 1 shows an example of a crater shrinkage cavity in the weld crater, which was made with a mild steel flux-cored gas-shielded wire. It is not weld porosity, but rather is a naturally occurring phenomenon found in arc welding.
Feedability: This is the ability to consistently feed the spooled welding wire during the welding process. Feedability is probably the most common problem experienced when moving from MIG welding of steel to MIG welding of aluminum. Choosing a welding wire of high quality and consistency, such as the AlcoTec product, can effectively minimize feedability problems. AlcoTec wire has exceptional surface smoothness, extremely tight diameter control, and excellent lubricity, created through the use of a patented feedability process. Feedability is a far more significant issue with aluminum than steel. This is primarily due to the difference between the material's mechanical properties. Steel welding wire is rigged, can be fed more easily over a further distance, and can withstand far more mechanical abuse when compared to aluminum. Aluminum is softer, more susceptible to being deformed or shaved during the feeding operation, and consequently, requires far more attention when selecting and setting up a feeding system for MIG welding. Feedability problems often express themselves in the form of irregular wire feed or as burn-backs (the fusion of the welding wire to the inside of the contact tip). In order to prevent excessive problems with feedability of this nature, it is important to understand the entire feeding system and its effect on aluminum welding wire. If we start with the spool end of the feeding system, we must first consider the brake settings. Brake tension should be adjusted to a minimum. Only sufficient brake pressure to prevent the spool from free-wheeling when welding has stopped, is required. Electronic braking systems and electronic/mechanical combinations have been developed to provide more sensitivity within the braking system. Inlet and outlet guides, as well as liners, which are typically made from metallic material for steel welding, must be made from a non-metallic material such as nylon, to prevent abrasion and shaving of the aluminum wire. Drive rolls have been developed with U-type contours, edges that are chamfered and not sharp, that are smooth, aligned, and provide correct drive roll pressure. Excessive drive roll pressure can deform the aluminum wire and increase friction drag through the liner and contact tip. Contact tip I.D. and quality are of great importance. We are seeing the availability of contact tips made specifically for aluminum welding that have smooth internal bores and are absence of sharp burrs on the inlet and outlet ends of the tips which can easily shave the softer aluminum alloys.
Aluminum welding wire is used in both push and pull feeder systems; however, limitations are recognized dependent on application and feeding distance. Push-pull feeder systems for aluminum have been developed and improved upon to help overcome feeding problems and may be used on more critical/specialized operations such as robotic and automated applications. More recently, the planetary drive push-pull system (ESAB Mongoose System) has become popular for aluminum welding, providing an extremely positive feeding system capable of delivering aluminum wire over greater distances with minimum burn-back problems.
Porosity: Porosity is a result of hydrogen gas becoming entrapped within solidifying aluminum during welding and leaving voids in the completed weld. Hydrogen is highly soluble in molten aluminum (as seen in Fig 1) and for this reason, the potential for excessive amounts of porosity during arc welding of aluminum is considerably high. Hydrogen can be unintentionally introduced during the welding operation through contaminants within the welding area such as hydrocarbons and/or moisture. Hydrocarbons may be found on plate or welding wire that has been contaminated with such items as lubricants, grease, oil, or paint. It is important to understand the methods available for the effective removal of hydrocarbons and to incorporate the appropriate methods into the welding procedure. Moisture (H2O) contains hydrogen and may be introduced to the welding area through water leaks within the welding equipment cooling system, inadequately pure shielding gas, condensation on plate or wire from high humidity and change in temperature (crossing a dew point), and/or hydrated aluminum oxide.
Other areas of potential contamination problems are associated with material preparation. Cutting or grinding methods that may deposit contaminants on to the plate surface or sub-surface, cutting fluids, grinding disc debris, and saw blade lubricants are all areas of concern and should be closely evaluated as a controlled element of the welding procedure and not changed without revalidation. Certain types of grinding discs, for example, can deposit particles within the aluminum which will react during welding and cause major porosity problems.
Correct cleaning of the aluminum parts prior to welding, use of proven procedures, well maintained equipment, high quality shielding gas, and a welding wire that is free from contamination, all become very important variables if low porosity levels are desirable. Porosity is typically detected by radiographic testing of completed welds. However, there are other methods which can be used without radiography equipment to evaluate porosity levels on test plates. The nick break test for groove welds and the fracture break test for fillet welds can be extremely useful on test plates when evaluating a new cleaning method and during preliminary procedure development.
Cracking: A problem that can be easily encountered when aluminum welding is solidification cracking or the hot cracking problem. This form of cracking in aluminum is typically caused by a combination of metallurgical weaknesses of the weld metal as it solidifies with transverse stress applied across the weld. The metallurgical weakness is often a result of the wrong filler alloy / base alloy mixture, referred to as the critical chemistry range and the transverse stress from shrinkage during solidification of the weld. These cracks are called hot cracks because they occur at temperatures close to the solidification temperature. In order to reduce the possibility of hot cracking, we need to understand two issues: the reduction of transverse stresses across the weld and the avoidance of critical chemistry ranges in the weld. The reduction or redistribution of stresses on the weld during solidification may be achieved by the reduction of restraint which may be a result of excessive fixturing, and/or also through the use of filler alloys that have lower melting and solidification points than the base alloy and/or which have smaller freezing temperature ranges. The method of ensuring the avoidance of the critical chemistry range is based on the understanding of the relative crack sensitivity curves as seen in Fig 2. This chart shows the crack sensitivity curves for the most common weld metal chemistries developed during the welding of the base alloy materials.
As can be seen from the chart, copper in aluminum alloys (Al-Cu) exhibits a wide range of crack sensitivity.
Magnesium in aluminum from 0.5 up to 3.0%, produces a weld metal composition that is crack sensitive and should be avoided. Another issue relating to the aluminum magnesium base alloys, which is not directly related to the crack sensitivity chart, but is a very important factor, must be addressed. As a rule, the Al – Mg base alloys with less than 2.8% Mg content can be welded with either the Al – Si (4xxx series) or the Al – Mg (5xxx series) filler alloys dependent on weld performance requirements. The Al – Mg base alloys with more than about 2.8% Mg typically cannot be successfully welded with the Al – Si (4xxx series) filler alloys. This is due to a eutectic problem associated with excessive amounts of magnesium silicide (Mg2Si) developing in the weld structure, decreasing ductility and increasing crack sensitivity.
Perhaps the most common problem associated with hot cracking and the critical chemistry issue is found with the aluminum, magnesium, silicon alloys (Al - Mg2Si) or 6xxx series base alloys as they are known. As purchased, the 6xxx series base alloys, 6061 for example, contain around 1.0% magnesium silicide (Mg2Si), and as can be seen in the chart, this is the worst condition, providing maximum crack sensitivity. It should be noted that these base materials, when plasma cut, will typically produce solidification cracking along their cut edge. The requirement for the removal of 1/8 inch of the base material mechanically from the cut edge after plasma cutting (if the edge is to be incorporated into a welded joint) is a standard / code requirement.
These base alloys will typically crack if not welded with adequate filler alloy additions in order to change their chemistry and reduce their hot cracking sensitivity. The 6xxx series alloys can be welded with 4xxx series (Al – Si) or 5xxx series (Al – Mg) filler alloys dependent on weld performance requirements. The main consideration is to adequately dilute the Mg2Si percentage in the base material with sufficient filler alloy to reduce weld metal crack sensitivity. Care must also be taken when welding the 6xxx series base alloy with the 5xxx (Al – Mg) filler alloys to ensure sufficient additions of filler alloy to prevent the Al – Mg crack sensitivity chemistry range. These types of chemistry cracking problems are usually addressed through weld joint design to ensure maximum filler alloy dilution through increased bevel angles and joint spacing.
Another type of cracking in aluminum is crater cracking or termination cracking. This type of cracking is experienced at the end of the weld and is best reduced through the use of weld stopping techniques. One method is to remove the crater from the functional area of the weld by the use of run-off plates that are mechanically removed after welding. Other usually more practical methods are to reduce the weld pool size just before the arc is extinguished, so that there is no longer enough shrinkage stress to form a crack.
Some modern welding machines have been developed for aluminum welding and have a built in crater fill function that is designed to terminate the weld in a gradual manner thus preventing a crater from forming at weld termination thereby eliminating the crater cracking problem.
Filler Alloy Selection: When welding steel, the selection of a filler alloy is often based on the tensile strength of the base alloy alone. The selection of a filler alloy for aluminum is typically not that simple and is usually not based solely on the tensile strength of the completed weld. With aluminum there are a number of other variables which need to be considered during the filler alloy selection process. The understanding of these other variables and their effect on the completed weldment are of extreme importance.
When choosing the optimum filler alloy, both base alloy type and desired performance of the weldment must be of prime consideration. What is the weld subjected to, and what is it expected to do? The most reliable method of choosing an aluminum filler alloy for evaluation is by using the AlcoTec filler alloy selection chart. The filler alloy selection chart is based on the application variables of the completed weld and rates each variable independently. Some understanding of how the recommendations for filler alloy evaluation within the chart were developed and the possible results of selecting the incorrect filler alloy may prove useful.
The variables which need to be considered during filler alloy selection are:
Ease of Welding (relative freedom from weld cracking) - This is based on the filler alloy / base alloy combination, its relative crack sensitivity and the critical chemistry ranges as discussed in the last section. This rating is based on the probability of producing a crack sensitive filler alloy / base alloy combination.
Strength of the Weld – This rating is based on the ability of the filler alloy to meet or exceed the strength of the as-welded joint. Most often with aluminum the heat affected zone (HAZ) of a groove weld dictates the strength of the joint, and often many filler alloys can satisfy this strength requirement. Unlike groove welds, the joint strength of fillet welds is based on shear strength that can be affected considerably by filler alloy selection. Fillet weld strength is largely dependent on the composition of the filler alloy used to weld the joint. Typically, the 4xxx series filler alloys have lower ductility and provide less shear strength in fillet joints. The 5xxx series fillers typically have more ductility and can provide close to twice the shear strength of a 4xxx series filler alloy in some circumstances.
Weld Ductility – Ductility is a property that describes the ability of a material to plastically flow before fracturing. Fracture characteristics are described in terms of ability to undergo elastic stretching and plastic deformation in the presence of stress risers (weld discontinuities). Increased ductility ratings for a filler alloy indicate greater ability to deform plastically and to redistribute load thereby decreasing the crack propagation sensitivity. Ductility may be a consideration if forming is to be performed after welding, or if the weld is going to be subjected to impact loading.
Service Temperature - When considering service at temperatures above 150 Deg F, we must consider the use of filler alloys that can operate at these temperatures without any undesirable effects to the welded joint. Aluminum / magnesium alloys of over 3 % Mg, that are exposed to elevated temperature, can produce segregation of magnesium at the grain boundaries of the material. This is an undesirable condition which can result in premature failure of a welded component. Consequently, both base alloys and filler alloys with less than 3 % Mg have been developed for high temperature applications.
Corrosion Resistance - Most unprotected aluminum base alloy filler alloy combinations are quite satisfactory for general exposure to the atmosphere. In cases where a dissimilar aluminum alloy combination of base and filler is used, and electrolyte is present, it is possible to set up a galvanic action between the dissimilar compositions. Corrosion resistance can be a complex subject when looking at service in specialized highly corrosive environments and may necessitate consultation with engineers within this specialized field.
Color Match After Anodizing - The color of an aluminum alloy when anodized depends on its composition. Silicon in aluminum causes a darkening of the alloy when chemically treated during the anodizing process. If 5% silicon alloy 4043 filler is used to weld 6061, and the welded assembly is anodized, the weld becomes black and is very apparent. A similar weld in 6061 with 5356 filler does not darken during anodizing, so a good color match is obtained.
Post Weld Heat Treatment – Typically, the common heat treatable base alloys, for example 6061-T6, lose a substantial proportion of their mechanical strength after welding. In order to return the base material to its original strength, it may be an option to perform post weld heat treatment. If post weld heat treatment is the option, it may be necessary to evaluate the filler alloy used with regard to its ability to respond to the heat treatment. Filler alloy 4643, for example, was developed for welding the 6xxx series base alloys and developing high mechanical properties in the postweld heat-treated condition. Other filler alloys have been developed that are designed to respond to thermal postweld treatment, particularly for use with the heat-treatable casting alloys. The important thing to remember here is that the common filler alloys may not respond or even respond adversely to postweld thermal treatments.
Conclusion: I have attempted to provide information within this article that I hope will assist with the understanding of the differences and concerns when welding aluminum compared to other materials. The successful welding of aluminum is not so much difficult as it is different. An understanding of the differences, is in my opinion, the first step in producing successful welding procedures for this somewhat unique material which is continuing to advance in use within the welding fabrication industry.
Welding defects can be said to be the irregularities formed in a given weld metal as a result of incorrect welding patterns, wrong welding process, or due to poor welding skills from the welder's part. Weld flaws may come in different sizes, shapes, and degrees of severity.
There are different types of welding defects that can transpire during the welding process. From porosity and cracking, to burn through and undercut, each has several causes.
However, regardless of the application and material on which they occur, one thing remains true to all of them; they're common, costly, cause downtime and loss of productivity.
Luckily enough, there are various remedies that can help welders minimize these welding defects. In this article, we shall be discussing the seven most common welding defects, causes, and remedies plus 2 others.
Keep reading!
What are welding defects?
Welding defects/flaws can be defined as weld surface irregularities, imperfections, discontinuities, or inconsistencies that are formed in welded parts.
These defects differ from the desired weld bead size, shape, and quality. Welding defects could occur either from the outside or inside the weld metal.
Defects in weld joints could cause the rejection of parts and assemblies, an increase in the cost of maintenance, a reduction in performance and could cause catastrophic failures posing the risks of loss of life and property.
Welding defects and remedies
Mistakes sometimes occurs during a welding process. These could lead to different forms of welding defects. As a guide, We present to you the seven most common welding defects and their preventive measures.
1. Porosity
Porosity usually occurs as a result of weld contamination. This happens when gas is trapped inside or along the surface of the weld metal. Just like other weld defects, Porosity results in weak welds that may easily collapse.
• Causes of Porosity:
Often, Contaminated or inadequate shielding gas is the common cause of porosity.
However, Porosity could also be caused by using too high gas flow, longer arc, inadequate electrode deoxidant, and the presence of paint, rust, grease, or oil.
At the same time, having a dirty base metal or extending the welding far beyond the nozzle could cause porosity.
Additionally, air currents from cooling fans may contaminate the shielding gas envelope around the weld-puddle, thereby causing porosity.
Another common cause of this welding flaw is poor seal (loose-fitting) in the shielding gas channel.
• Remedies for Porosity:
You can remedy the porosity of a weld by; cleaning the materials to be welded before you begin welding, using correct arc distance, employing the proper welding technique, and using the right electrodes.
Again, ensure that there is adequate gas flow and replace any gas hoses that may be causing leaks. Also, when welding outside or in drafty areas, place a welding screen around the work area. This will help ameliorate porosity issues.
2. Undercutting
Undercutting is a crater or groove that is formed near the toe of the weld. In this case, the weld metal fails to fill-in the grooved area resulting in a weak-weld that is liable to cracking along the toes.
• Causes of Undercutting:
Crater Defect In Welding
Wrong filler metal, excessive heat, fast weld speed, as well as poor welding technique, may all leads to undercut welding defect on a welding joint.
Also, very high weld current, incorrect use of shielding gas and using the wrong electrode could cause undercuts.
• Remedies for Undercutting:
Undercutting in welding can be avoided by employing the right welding technique that does not involve excessive weaving.
Lowering the arc length and minimizing the travel speed of the electrode can also help prevent undercutting.
Another remedy to undercutting problem is adjusting the angle of the gun to point directly towards the weld joint.
3. Burn Through
As the name implies, burn through occurs when the weld metal penetrates through the base metal, burning through it. This kind of welding flaw is most common with soft or thin metals, especially those that are 1/4″ or less. Also too much weld penetration can often lead to burn through.
• Causes of burn through:
The primary cause of burn through is excessive heat. Also having too large root opening on the weld joint can results in burn through.
• Remedies for burn through:
When burn through occurs, the easiest way to rectify the problem is to lower the voltage and the wire feed speed.
Also increasing the travel pace can help remedy the problem, especially when welding on aluminum material.
Increasing the wire extension and using a weaving technique while welding can also help minimize the potential for burn through.
4. Incomplete Penetration
Incomplete joint penetration (lack of penetration) happens when there is a shallow fusion between the base metal and filler metal, rather than full penetration of the joint. It results in a gap, cracks, or even joint failure.
• Causes of incomplete joint penetration:
Incomplete joint penetration could occur when the groove you are welding is too narrow, and the weld metal does not reach the bottom of the joint.
Improper joint preparation and insufficient heat input are the two primary causes of lack of penetration. Improper shielding gas mixture and welding wire diameter can also be a factor.
Also, if you leave too much space between the two metals you are welding, the metals will not melt together on the first pass and hence results in incomplete penetration.
• Remedies for incomplete penetration:
There are a number of remedies for incomplete joint penetration; this includes; using higher wire feed speed and voltage, reducing the travel pace to allow more weld metal penetrates through the joint, and proper joint design and preparation.
The joint should be prepared in such a way to allow the welder to maintain the proper wire extension and still access the bottom of the weld joint. Again, ensure that ‘the wire type and diameters' and ‘the gas and the gas mixture' are compatible.
5. Cracks
Weld Cracks are the most serious type of welding defects. Weld Cracks are not acceptable in the welding industry.
However, a crack may occur just about everywhere in a weld; in the weld metal, on the plate next to the weld metal, or anyplace affected by intense heat.
The three major types of weld cracks are: Hot cracks, cold cracks, and crater cracks
• Causes of weld cracks:
Weld Crack could be caused by so many things such as base metal contamination, poor joint design, failure to preheat before welding, low welding current, high welding speed, using hydrogen when welding ferrous materials and welding at too high voltage.
Description: Need to set a deadline or some kind of time for whatever reason? Use a countdown timer for that! This simple but very useful widget allows you to set the time you want it to countdown to. Easy to set and start, you can have a countdown timer ready for any occasion or time you may need it. Countdown Timer allows multiple (up to five) user defined times and to be counted down simultaneously. Each timer can be given a name. Each timer remembers its name and time from the previous session the app was run. It is useful for sports, cooking, and other events. Windows desktop gadgets tagged with 'timer' categories. Alarm clock amazon analog clocks astronomy battery bing brightness calculator calendar christmas clipboard countdown cpu digital clocks flag flipped clock gadgets set game google graphics guitar hdd horoscope internet ip iphone. How to install Windows 7 gadgets How to. Microsoft windows 7 countdown timer gadget. Alarm clock amazon analog clocks astronomy battery bing brightness calculator calendar christmas clipboard countdown cpu digital clocks flag flipped clock gadgets set game google graphics guitar hdd horoscope internet ip iphone laptop mail map memory music network notepad player pocker processor quran radio ram reboot restart rss search.
• Remedies for weld cracks:
You can prevent this type of weld flaw by using the right metal. Proper joint design and preparation is also another way to prevent cracking. Crater cracking can be prevented by using a backfilling technique. Right Selection of filler metal and shielding gas can also help prevent cracking problems.
6. Incomplete Fusion
Incomplete fusion occurs when the weld metal fails to properly fuse with the base metal, or when the individual weld beads don't fuse together. This type of weld defect is also referred to as cold lap.
• Causes of incomplete fusion

Incorrect gun angle is the most common cause of incomplete fusion. However, contaminants on the base metal and insufficient heat can also cause this weld defect.
In some instances, too short arc length, very high travel speed, too low welding amperage or when the electrode size is too small for the thickness of the metal you are welding, all could result to incomplete fusion.
• Remedies for incomplete fusion:

The very first thing to do to prevent this weld flaw is to properly clean the base metal before you start the welding; make sure that the base metal is free of oil, grease, dirt or other debris.
Make sure the weld angle is between 0 to 15 degrees; this will allow you to fully access the groove of the weld.
Also, for joints that require weaving technique, holding the arc on the sidewall for some time is very vital to help prevent this type of defect. Ensure that there is enough heat input to coalesce the base metal and the weld metal fully.
7. Slag Inclusions
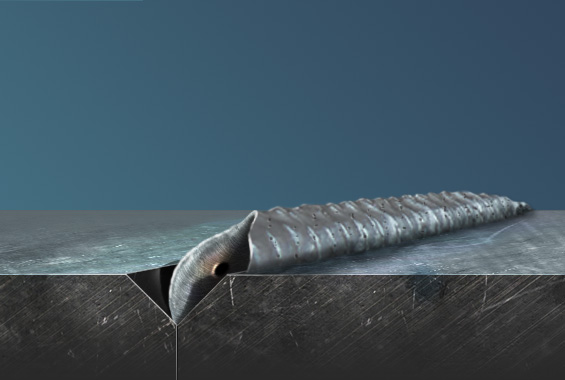
Slag is the waste material that is usually formed while welding, bits of this solid waste material may accidentally be incorporated into the weld and causes contamination.
• Causes of slag inclusions:
Some of the common causes of slag inclusions include failure to properly clean a welding pass before applying the next pass, incorrect welding angle, incorporation of flux from stick welding electrode, and too low welding amperage.
8. Warpage
Warpage is an unwanted distortion in the shape of a piece of metal. This occurs when the welder fails to properly control the expansion and contraction of the base material.
• Causes of warpage:
Warpage may arise when the welder clamps the welding joints too tightly, welding a piece of metal over and over again can also cause the metal to warp.
Crater In Mig Welding
When welding a T-joint, the vertical part of the ‘T' may sometimes pull itself towards the weld. Also, the more heat input you use, the more the chances you have to end up with a warpage.
• Remedies for warpage:
Warpage can be prevented by using only the required amount of heat. Opting for moderate travel speed and wire feed speed while welding can also help curtail the problem of warpage.
9. Overlap
overlap occurs when the weld face extends far above the weld toe. In this case, the weld metal rollout and forms an angle less than 90 degrees.
• Causes of Overlap
Overlap welding defect can arise when using large electrodes greater than the metal size. High welding current and the use of improper welding technique can also cause this defect.
• Remedies for Overlap
Overlap welding defect can be avoided by employing the correct welding Technique, using small Welding electrode and less welding has.
Conclusion
Crater Fill In Welding
Incorrect gun angle is the most common cause of incomplete fusion. However, contaminants on the base metal and insufficient heat can also cause this weld defect.
In some instances, too short arc length, very high travel speed, too low welding amperage or when the electrode size is too small for the thickness of the metal you are welding, all could result to incomplete fusion.
• Remedies for incomplete fusion:
The very first thing to do to prevent this weld flaw is to properly clean the base metal before you start the welding; make sure that the base metal is free of oil, grease, dirt or other debris.
Make sure the weld angle is between 0 to 15 degrees; this will allow you to fully access the groove of the weld.
Also, for joints that require weaving technique, holding the arc on the sidewall for some time is very vital to help prevent this type of defect. Ensure that there is enough heat input to coalesce the base metal and the weld metal fully.
7. Slag Inclusions
Slag is the waste material that is usually formed while welding, bits of this solid waste material may accidentally be incorporated into the weld and causes contamination.
• Causes of slag inclusions:
Some of the common causes of slag inclusions include failure to properly clean a welding pass before applying the next pass, incorrect welding angle, incorporation of flux from stick welding electrode, and too low welding amperage.
8. Warpage
Warpage is an unwanted distortion in the shape of a piece of metal. This occurs when the welder fails to properly control the expansion and contraction of the base material.
• Causes of warpage:
Warpage may arise when the welder clamps the welding joints too tightly, welding a piece of metal over and over again can also cause the metal to warp.
Crater In Mig Welding
When welding a T-joint, the vertical part of the ‘T' may sometimes pull itself towards the weld. Also, the more heat input you use, the more the chances you have to end up with a warpage.
• Remedies for warpage:
Warpage can be prevented by using only the required amount of heat. Opting for moderate travel speed and wire feed speed while welding can also help curtail the problem of warpage.
9. Overlap
overlap occurs when the weld face extends far above the weld toe. In this case, the weld metal rollout and forms an angle less than 90 degrees.
• Causes of Overlap
Overlap welding defect can arise when using large electrodes greater than the metal size. High welding current and the use of improper welding technique can also cause this defect.
• Remedies for Overlap
Overlap welding defect can be avoided by employing the correct welding Technique, using small Welding electrode and less welding has.
Conclusion
Crater Fill In Welding
While welding defects and discontinuities may arise due to the welder's poor welding skills, however, even the most skilled and experienced welders may in one way or another experience weld defects.
Crater Pipe In Welding
But the only way to stop these welding irregularities from negatively affecting productivity and increasing the cost of operations is by identifying and rectifying the problems as quickly as possible.